Why OEMs Should Integrate Virtual Sensors: A Comprehensive Guide
JM
Understanding Virtual Sensors
In the rapidly evolving world of technology, Original Equipment Manufacturers (OEMs) need to stay ahead of the curve. One way to do this is by integrating virtual sensors into their products. But what exactly are virtual sensors? Unlike traditional sensors that rely on physical components to gather data, virtual sensors use mathematical models and software algorithms to estimate measurements. This innovative approach offers multiple advantages, making them a worthwhile consideration for OEMs.
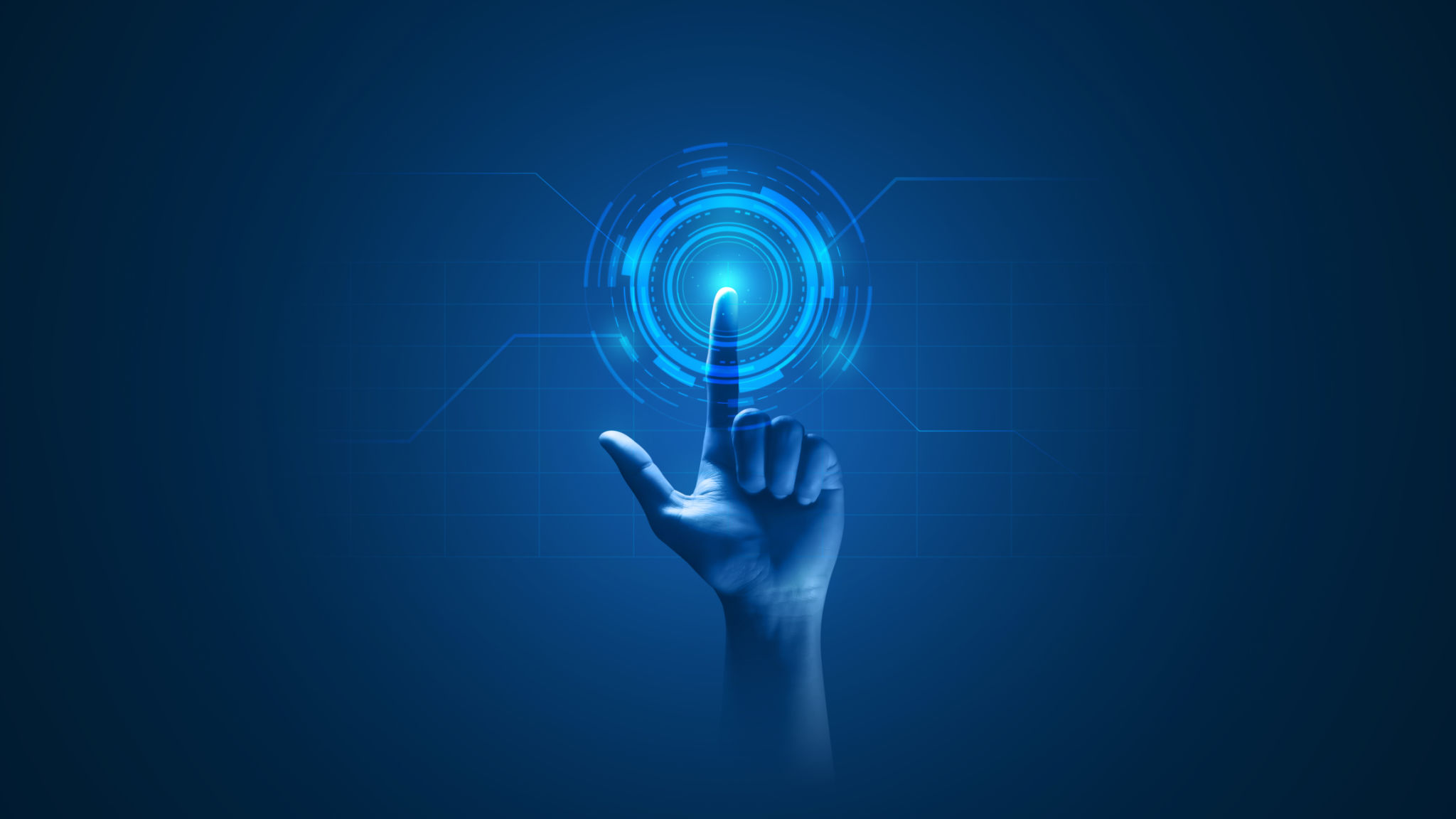
Benefits of Virtual Sensors
Virtual sensors provide several compelling benefits that can enhance product offerings. Firstly, they are cost-effective. Since they do not require physical components, OEMs can save on manufacturing costs while still delivering accurate data. Secondly, virtual sensors can be updated and refined through software updates, ensuring that products remain current and adaptable to new requirements without significant hardware changes.
Another advantage is their ability to provide real-time analytics and insights. By leveraging existing data, virtual sensors can offer predictive analytics that help in proactive decision-making. This is particularly beneficial in industries like automotive and manufacturing, where efficiency and safety are paramount.
Applications in Various Industries
The versatility of virtual sensors allows them to be applied across a wide range of industries. In the automotive sector, they can monitor engine performance and predict maintenance needs, reducing downtime and improving vehicle reliability. In manufacturing, virtual sensors can optimize production lines by tracking equipment performance and identifying potential issues before they result in costly failures.

Challenges and Considerations
Despite the numerous advantages, integrating virtual sensors comes with its own set of challenges. OEMs need to ensure the accuracy and reliability of the data generated by these sensors. This requires robust algorithms and continuous validation against physical measurements. Data security is another critical consideration, as these sensors often handle sensitive information that must be protected from breaches.
Moreover, OEMs must invest in skilled personnel who understand both the technical and analytical aspects of virtual sensors. Training and development are essential to maximize the benefits these sensors offer.
Steps for Integration
To successfully integrate virtual sensors, OEMs should follow a clear set of steps. Here is a simple guideline:
- Assessment: Evaluate the specific needs and capabilities of your product.
- Selection: Choose the right type of virtual sensors that align with your objectives.
- Implementation: Develop a plan for integrating the sensors into existing systems.
- Testing: Conduct thorough testing to ensure accuracy and reliability.
- Optimization: Continuously refine and update sensor algorithms for improved performance.
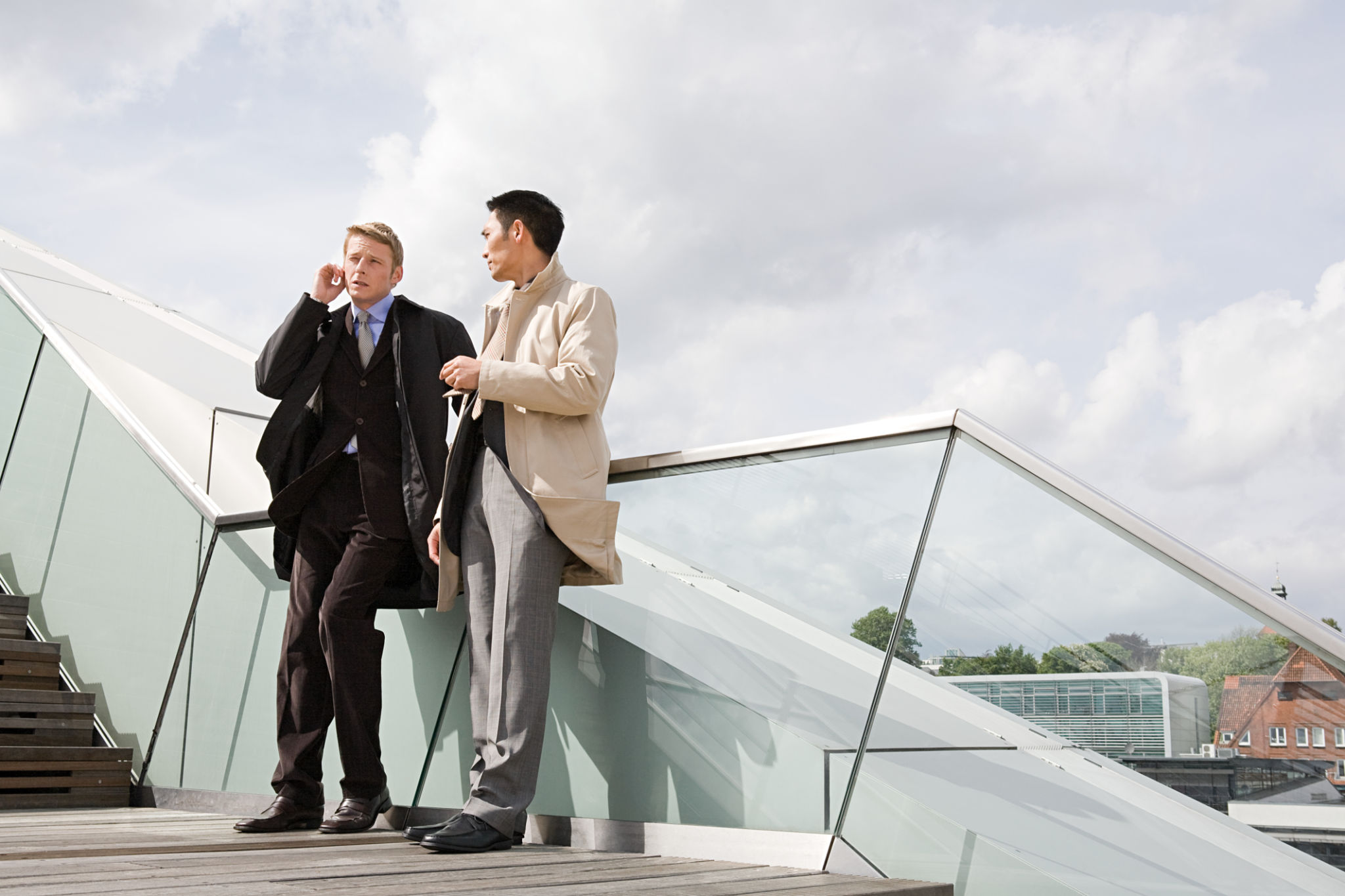
The Future of Virtual Sensors for OEMs
The future looks promising for OEMs that embrace virtual sensor technology. As industries move towards greater digitalization, the demand for smart products with advanced analytics will continue to rise. By integrating virtual sensors, OEMs can position themselves as leaders in innovation, offering customers cutting-edge solutions that deliver enhanced value and performance.
In conclusion, virtual sensors represent a transformative step for OEMs looking to modernize their offerings. With careful planning and execution, these sensors can provide significant benefits that drive efficiency, cost savings, and customer satisfaction.