Custom R&D Solutions: Transforming Mining Machinery with Virtual Sensors
JM
Revolutionizing Mining Machinery with Custom R&D Solutions
In the rapidly evolving world of mining, innovation is not just a competitive advantage—it's a necessity. Traditional methods are giving way to more advanced technologies that promise greater efficiency and safety. Among these innovations, custom research and development (R&D) solutions are playing a pivotal role in transforming mining machinery, particularly through the integration of virtual sensors.
Virtual sensors are digital tools that collect and analyze data from machinery without the need for physical sensing devices. They offer a cost-effective and flexible alternative to traditional sensors, providing real-time insights into machinery performance and health. This technological leap is making waves across the mining industry, enabling operators to make informed decisions that drive productivity and reduce downtime.
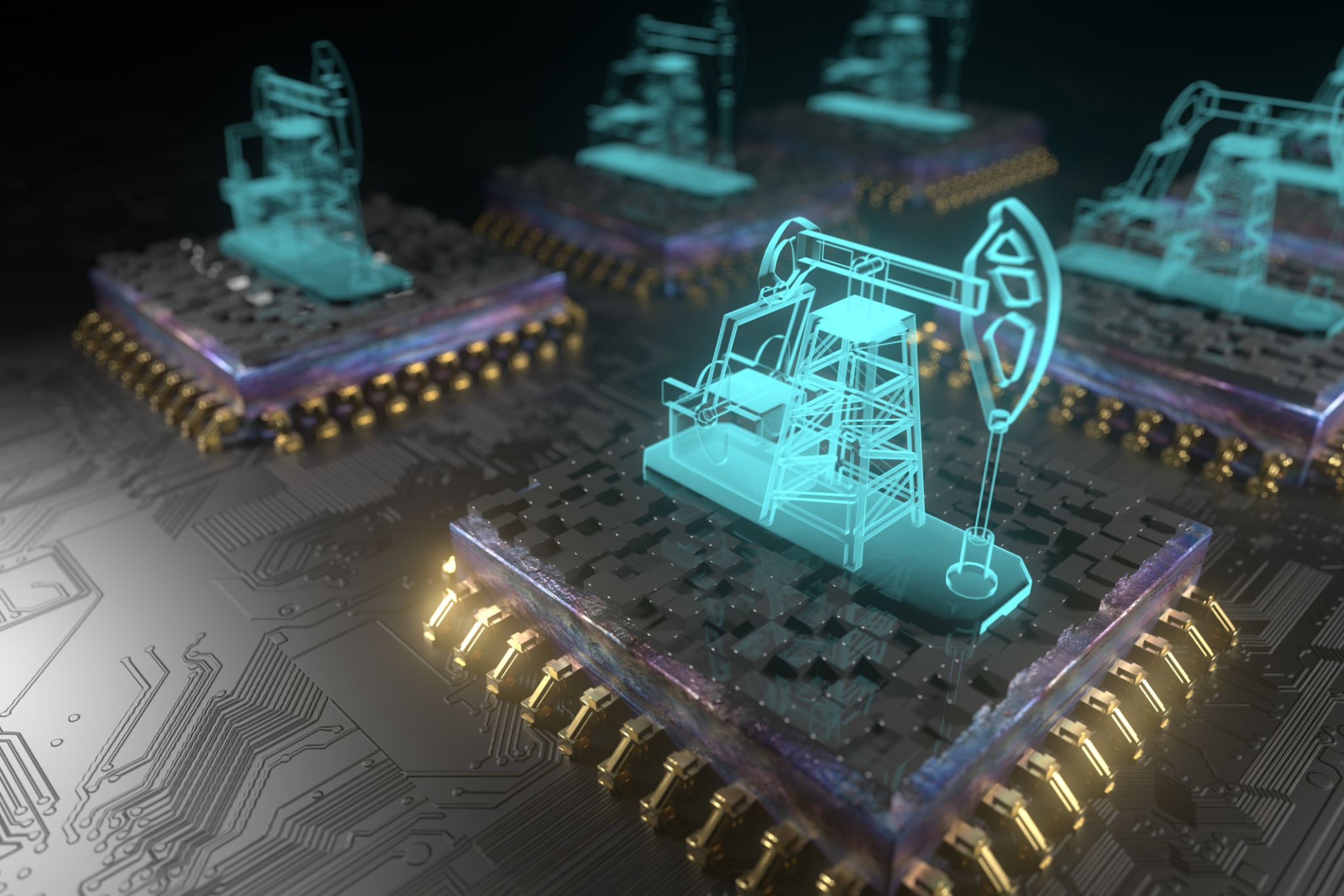
The Advantages of Virtual Sensors
One of the primary benefits of virtual sensors is their ability to provide continuous monitoring of equipment. Unlike physical sensors that may require regular maintenance or replacement, virtual sensors are software-based and can be updated remotely. This reduces maintenance costs and minimizes equipment downtime, resulting in more efficient operations.
Furthermore, virtual sensors offer enhanced data accuracy. By leveraging advanced algorithms and machine learning, these sensors can predict potential failures before they occur. This predictive capability allows operators to address issues proactively, avoiding costly repairs and extending the lifespan of equipment.
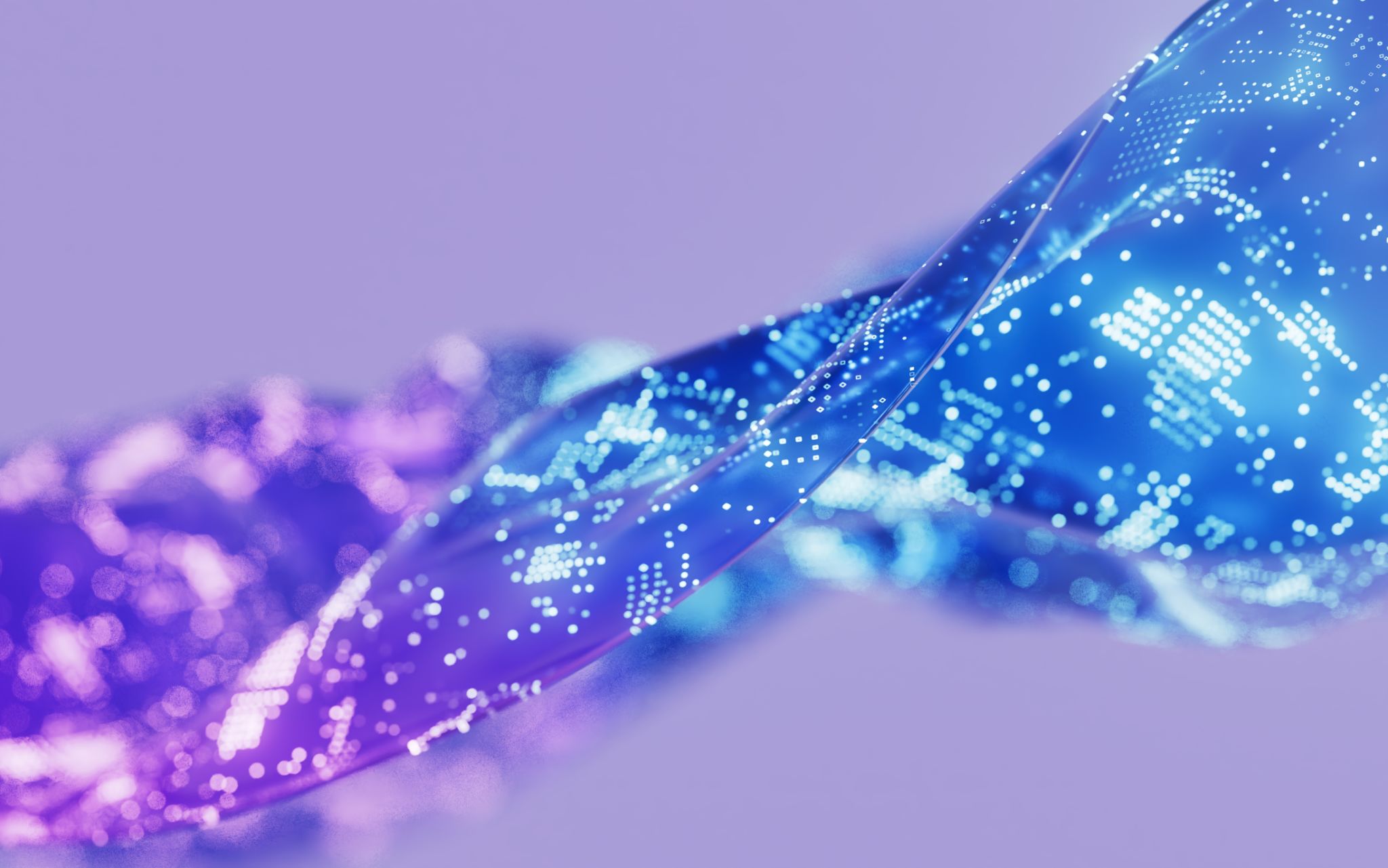
Custom R&D Solutions: Tailoring Technology to Industry Needs
Custom R&D solutions are essential in adapting virtual sensor technology to the unique challenges of the mining industry. Each mining operation is different, with specific machinery, environmental conditions, and operational goals. Customization ensures that the virtual sensors are optimized for these variables, providing relevant and actionable insights.
Developing a tailored solution involves several key steps:
- Assessment: Evaluating the specific needs and challenges of the mining operation.
- Design: Creating a bespoke virtual sensor system that aligns with operational requirements.
- Implementation: Integrating the custom solution into existing machinery with minimal disruption.
- Optimization: Continuously refining the system based on feedback and performance data.
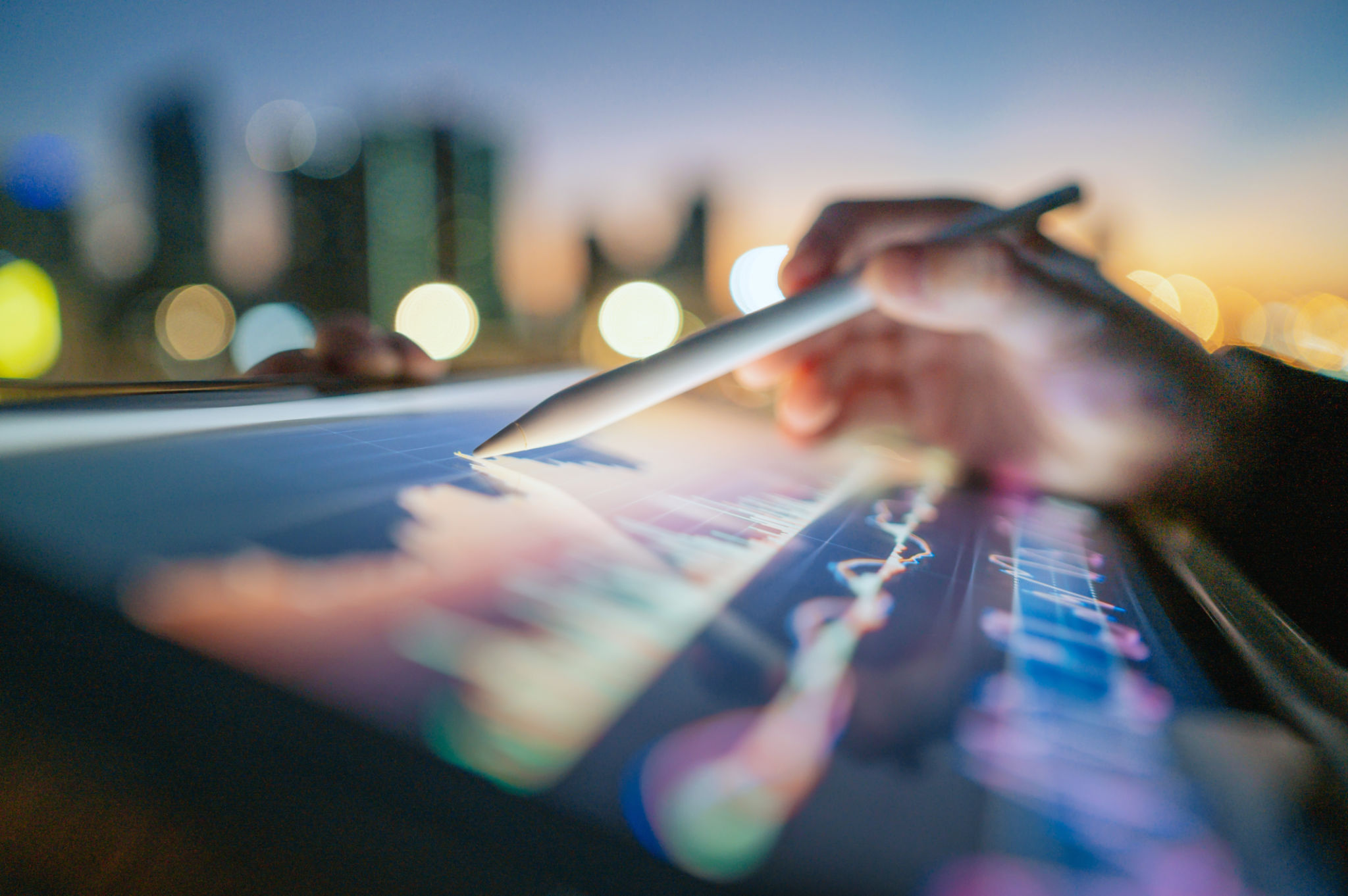
The Future of Mining Machinery
The integration of virtual sensors through custom R&D solutions is setting the stage for a new era in mining machinery. As these technologies become more sophisticated, they are expected to drive significant advancements in automation and AI-driven operations. This evolution promises not only increased efficiency but also enhanced safety measures, as machinery can autonomously detect and respond to hazardous conditions.
Looking ahead, the focus will be on further refining these technologies to ensure seamless interaction between human operators and automated systems. The goal is to create a harmonious working environment where technology augments human capabilities, leading to smarter and safer mining operations.
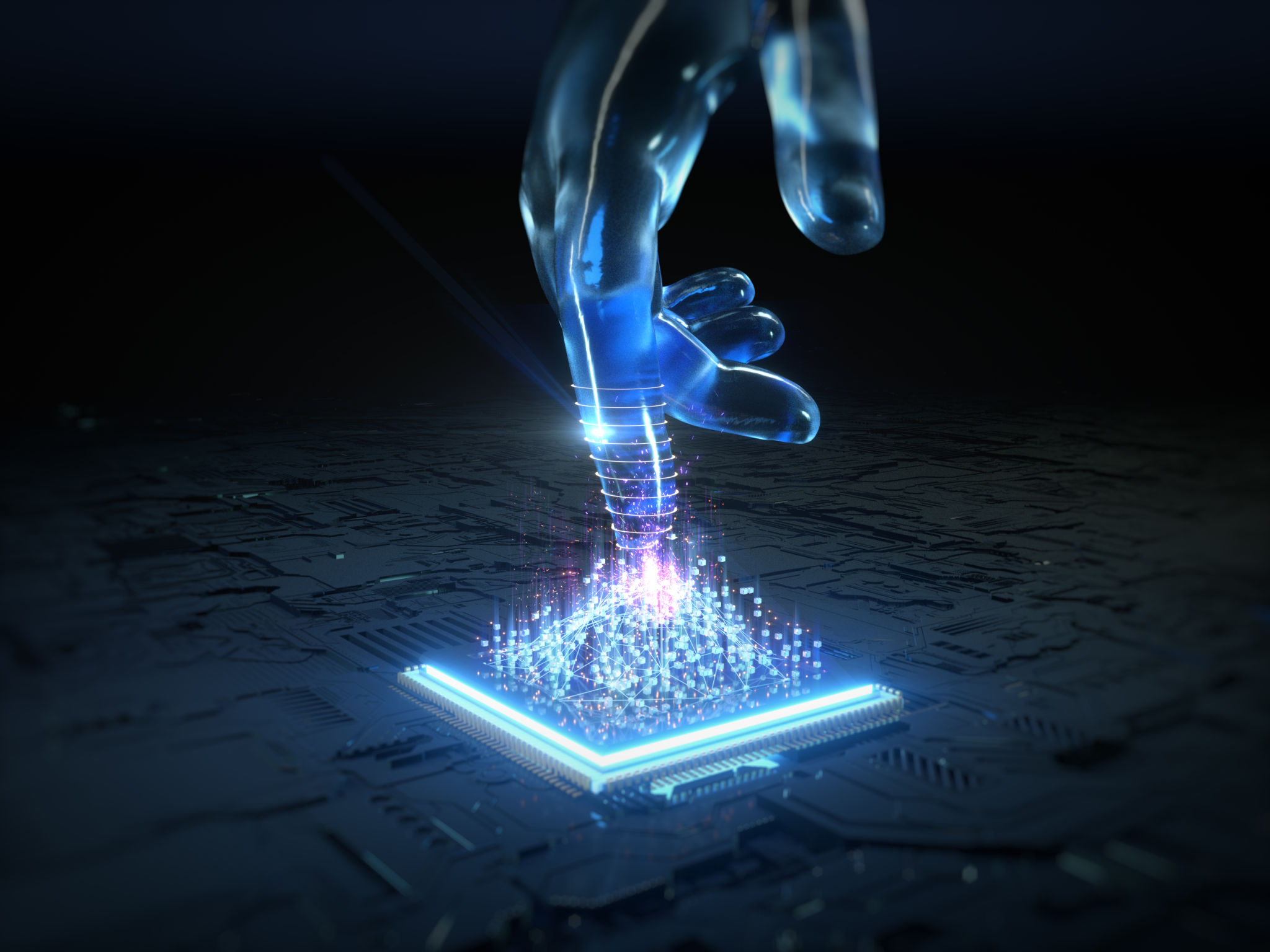
Conclusion
Custom R&D solutions are crucial in harnessing the full potential of virtual sensors for mining machinery. By providing tailored solutions that meet specific operational needs, these innovations pave the way for a more efficient, safe, and sustainable mining industry. As technology continues to advance, those who embrace these changes will be well-positioned to lead in this dynamic field.