Comparing Traditional vs Virtual Sensors in Material Handling Systems
JM
Understanding Traditional Sensors
In material handling systems, sensors play a crucial role in ensuring the smooth operation and efficiency of processes. Traditional sensors have been the backbone of these systems for decades. They are physical devices that detect changes in the environment, such as temperature, pressure, or motion, and provide real-time data to support decision-making.
Traditional sensors are known for their reliability and accuracy. They are often used in industrial settings where conditions are harsh and require robust equipment. These sensors can be tailored to specific applications, providing precise measurements that enhance the control and automation of material handling systems.
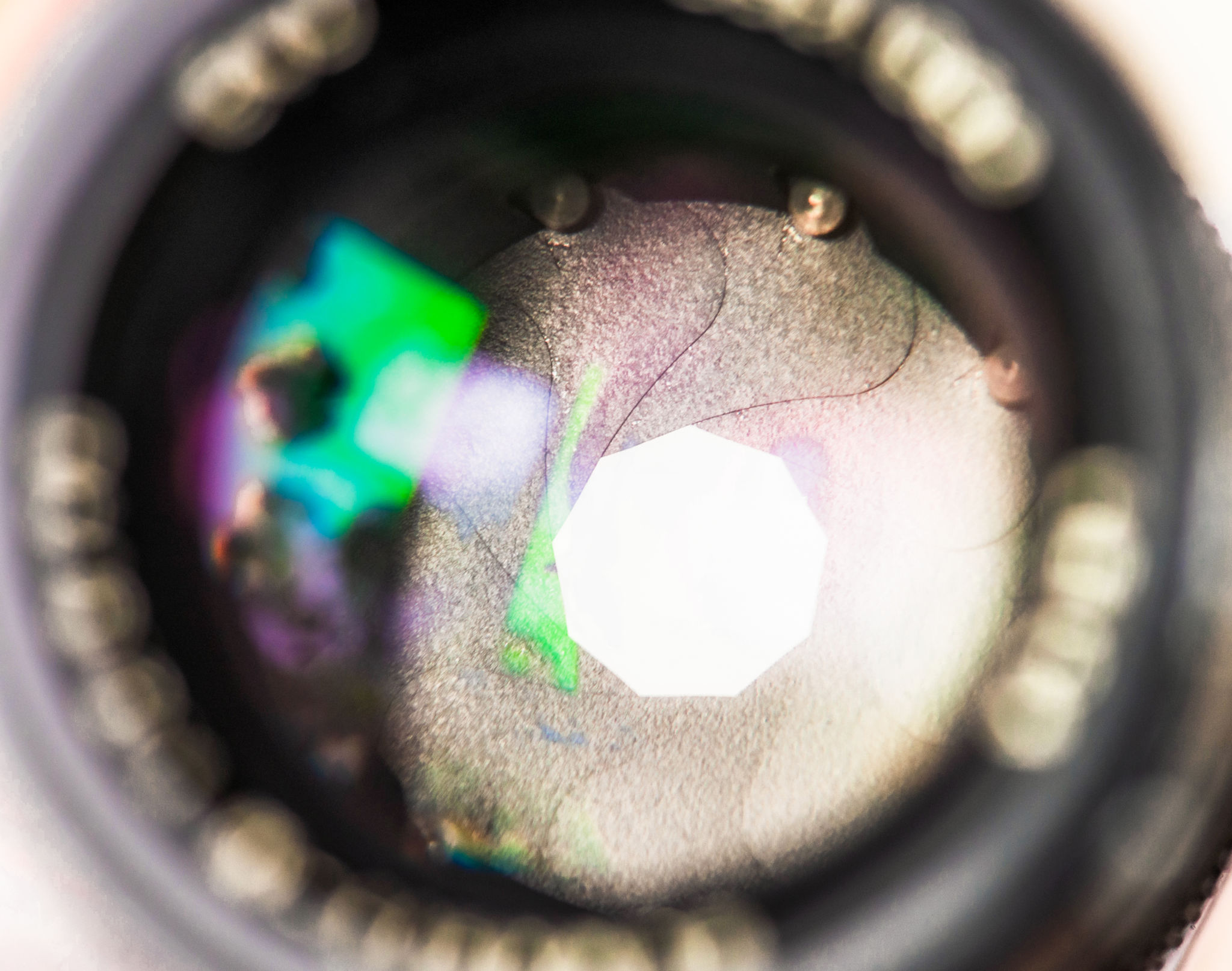
The Rise of Virtual Sensors
As technology advances, virtual sensors have emerged as a powerful alternative to traditional sensors. Unlike their physical counterparts, virtual sensors utilize software algorithms to estimate measurements based on existing data from other sources. This means they can provide valuable insights without the need for additional hardware.
Virtual sensors offer several advantages over traditional sensors. They can be more cost-effective, as they reduce the need for extensive physical installations. Additionally, because they are based on software, they can be easily updated and adapted to changing system requirements. This flexibility makes them an attractive option for modern material handling systems.
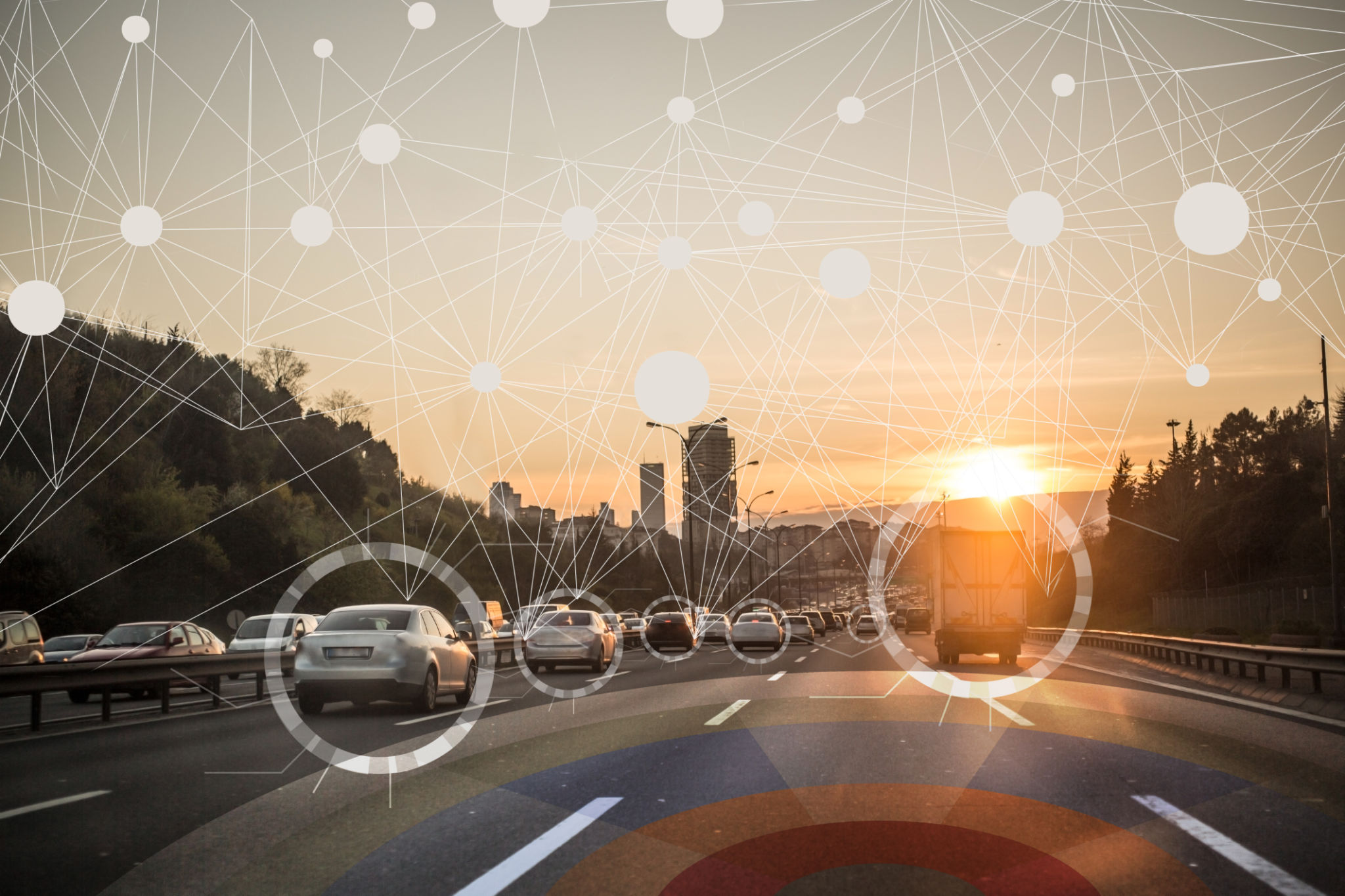
Comparing Accuracy and Reliability
When comparing traditional and virtual sensors, accuracy and reliability are essential factors to consider. Traditional sensors generally offer high precision, thanks to their direct measurement capabilities. However, they may require regular maintenance to ensure continued performance.
Virtual sensors, while potentially less accurate due to their reliance on indirect data, can still provide reliable estimates under the right conditions. Their strength lies in their ability to process vast amounts of data and identify patterns that might not be immediately apparent with traditional measurements.
Cost and Implementation Considerations
Cost is a significant consideration when deciding between traditional and virtual sensors. Traditional sensors often involve higher upfront costs due to the need for physical components and installation. Maintenance expenses can also add up over time.
On the other hand, virtual sensors typically require lower initial investment since they leverage existing data infrastructure. While the development of accurate algorithms can incur costs, the long-term savings from reduced hardware requirements and maintenance can be substantial.
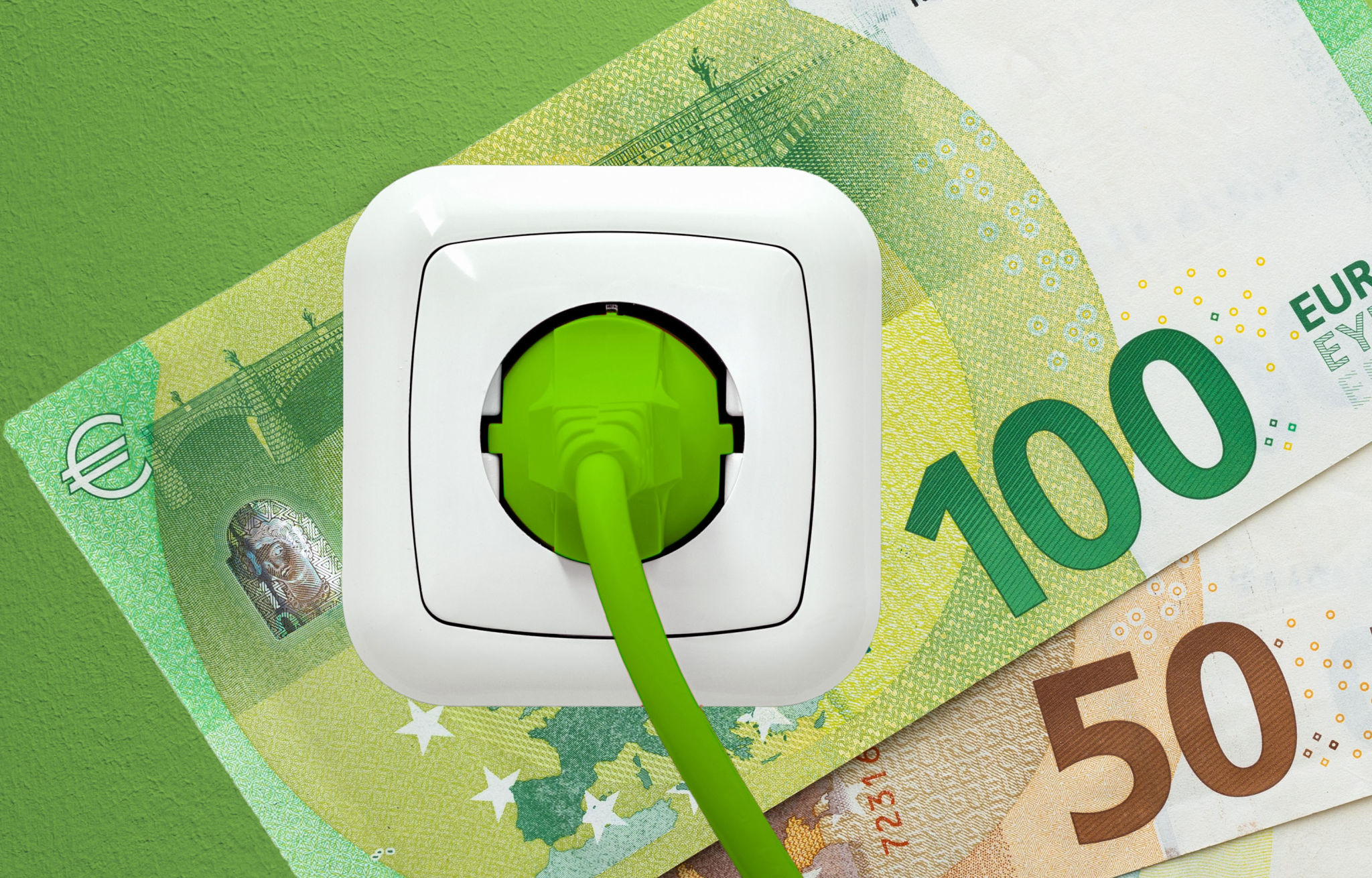
Integration and Scalability
Integration is another crucial aspect when comparing these two types of sensors. Traditional sensors might need extensive wiring and physical connections, which can complicate integration processes. This can be a limitation when scaling up operations or modifying system configurations.
Virtual sensors excel in integration and scalability due to their software-based nature. They can be seamlessly incorporated into existing systems and scaled without significant physical changes. This adaptability is particularly beneficial in dynamic environments where changes are frequent.
Applications in Material Handling
Both traditional and virtual sensors have unique applications in material handling systems. Traditional sensors are well-suited for applications requiring direct measurements, such as conveyor belt speed monitoring or temperature control in storage facilities.
Virtual sensors are increasingly used for predictive maintenance and process optimization. By analyzing data trends, they help anticipate equipment failures or optimize resource allocation, leading to improved operational efficiency.

Conclusion: Choosing the Right Sensor for Your Needs
The choice between traditional and virtual sensors depends on various factors, including accuracy requirements, budget constraints, and system flexibility. While traditional sensors offer precision and reliability in specific applications, virtual sensors provide innovative solutions with greater adaptability and cost-efficiency.
Ultimately, the decision should be based on a comprehensive evaluation of your material handling system's specific needs and goals. By carefully considering these factors, businesses can harness the power of both sensor types to enhance their operations and achieve optimal performance.