Case Study: How Simulation Modeling Improved Mining Machinery Performance
JM
Introduction to Simulation Modeling in Mining
In the realm of mining, efficiency and performance are key to success. The industry constantly seeks innovative methods to enhance machinery performance, reduce costs, and increase productivity. One such method is simulation modeling, a powerful tool that allows mining companies to visualize and optimize their operations without the need for physical trials.
Simulation modeling involves creating a digital replica of mining processes and machinery, enabling stakeholders to test various scenarios and configurations. This approach not only saves time but also reduces risks associated with physical testing. Let's explore a case study where simulation modeling significantly improved mining machinery performance.
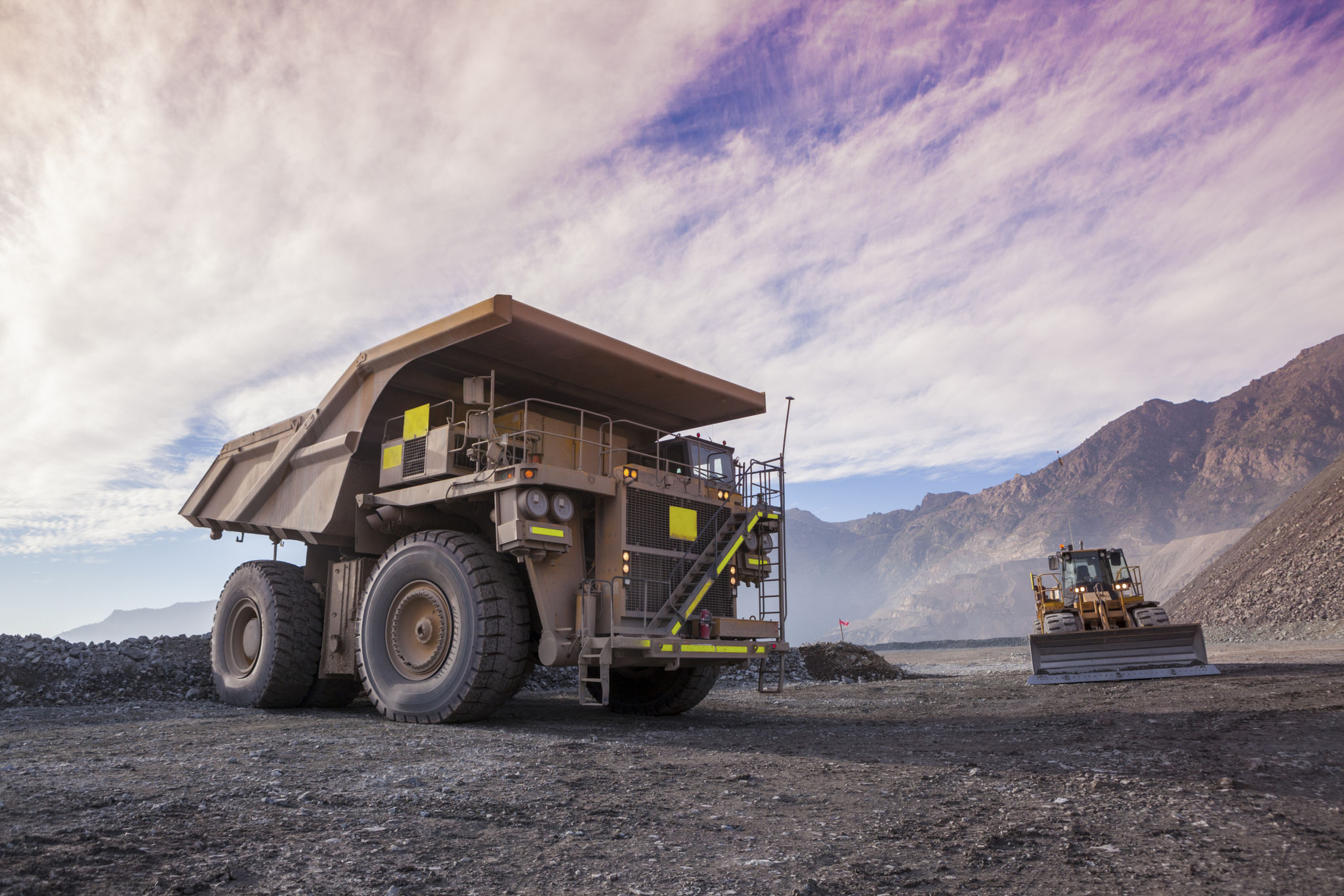
The Challenge: Enhancing Machinery Efficiency
A leading mining company faced challenges with the efficiency and performance of their machinery. The traditional trial-and-error approach was proving costly and time-consuming. They needed a solution that could provide insights into machinery operations and suggest improvements without disrupting their ongoing processes.
The company decided to adopt simulation modeling to tackle these challenges. By creating a digital twin of their machinery, they aimed to analyze various operational scenarios, identify bottlenecks, and implement strategic enhancements.
Implementing Simulation Modeling
The first step in this transformative journey was to gather comprehensive data on the machinery's current performance. This included metrics like energy consumption, operational speed, and downtime frequency. The data was then used to construct a detailed simulation model that accurately represented the machinery's behavior under different conditions.
With the model in place, the company ran several simulations to test different variables and configurations. This allowed them to identify inefficiencies and explore solutions without any physical trial runs. The simulation model also provided predictive insights, helping the company foresee potential issues and address them proactively.
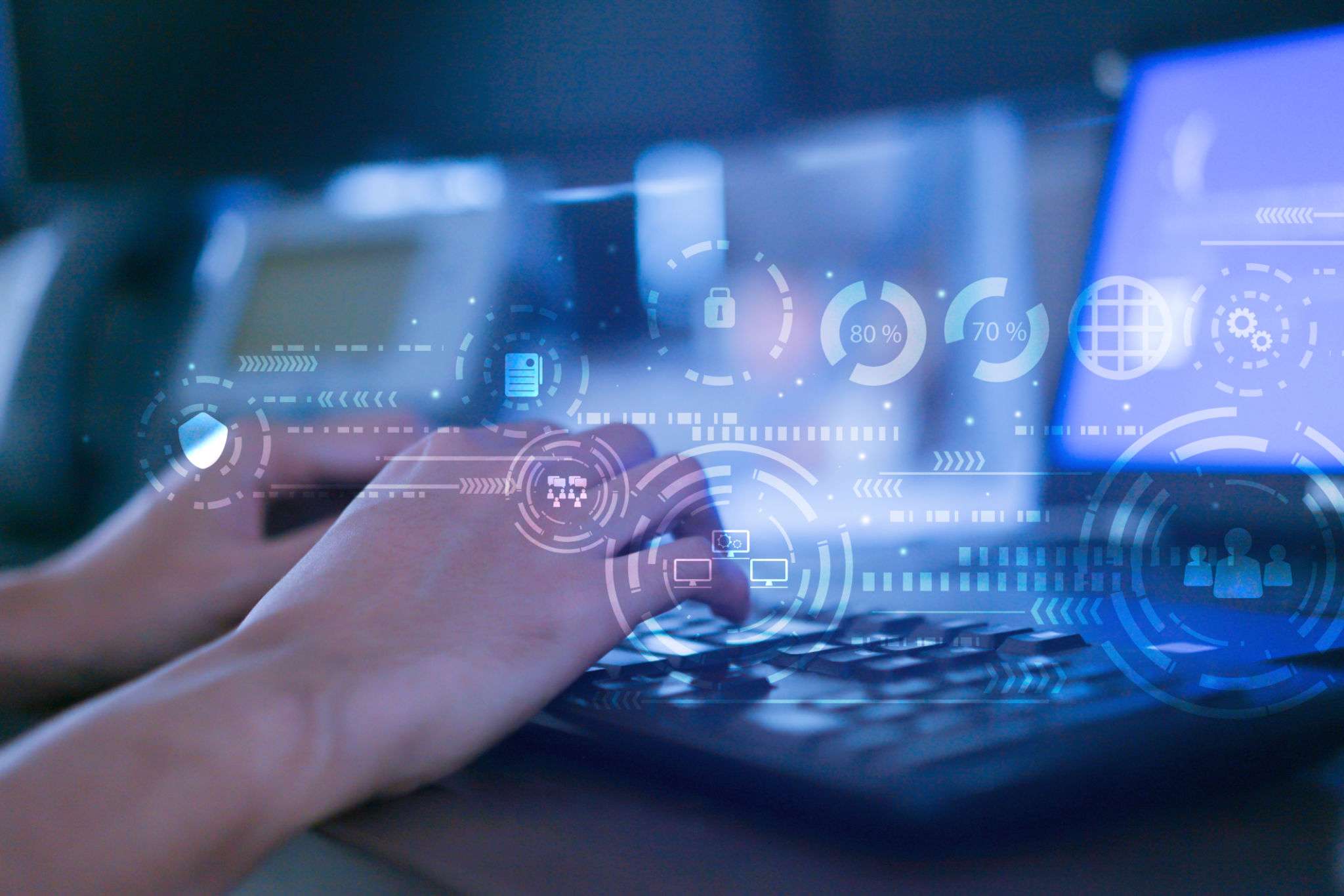
Results: Significant Performance Improvements
The results from the simulation model were promising. The company identified key areas where machinery performance could be improved. By implementing changes suggested by the simulations, they reduced energy consumption by 15% and increased operational speed by 20%. Additionally, the frequency of unexpected downtimes decreased significantly.
The use of simulation modeling not only resulted in immediate performance improvements but also fostered a culture of continuous optimization within the company. The ability to test new ideas quickly and safely encouraged innovation and empowered teams to make data-driven decisions.
Lessons Learned
This case study highlights several important lessons for the mining industry:
- Data is Key: Accurate and comprehensive data is crucial for building effective simulation models.
- Iterative Testing: The ability to test multiple scenarios quickly helps in identifying the most effective solutions.
- Predictive Insights: Simulation models offer valuable predictive insights that aid in proactive decision-making.
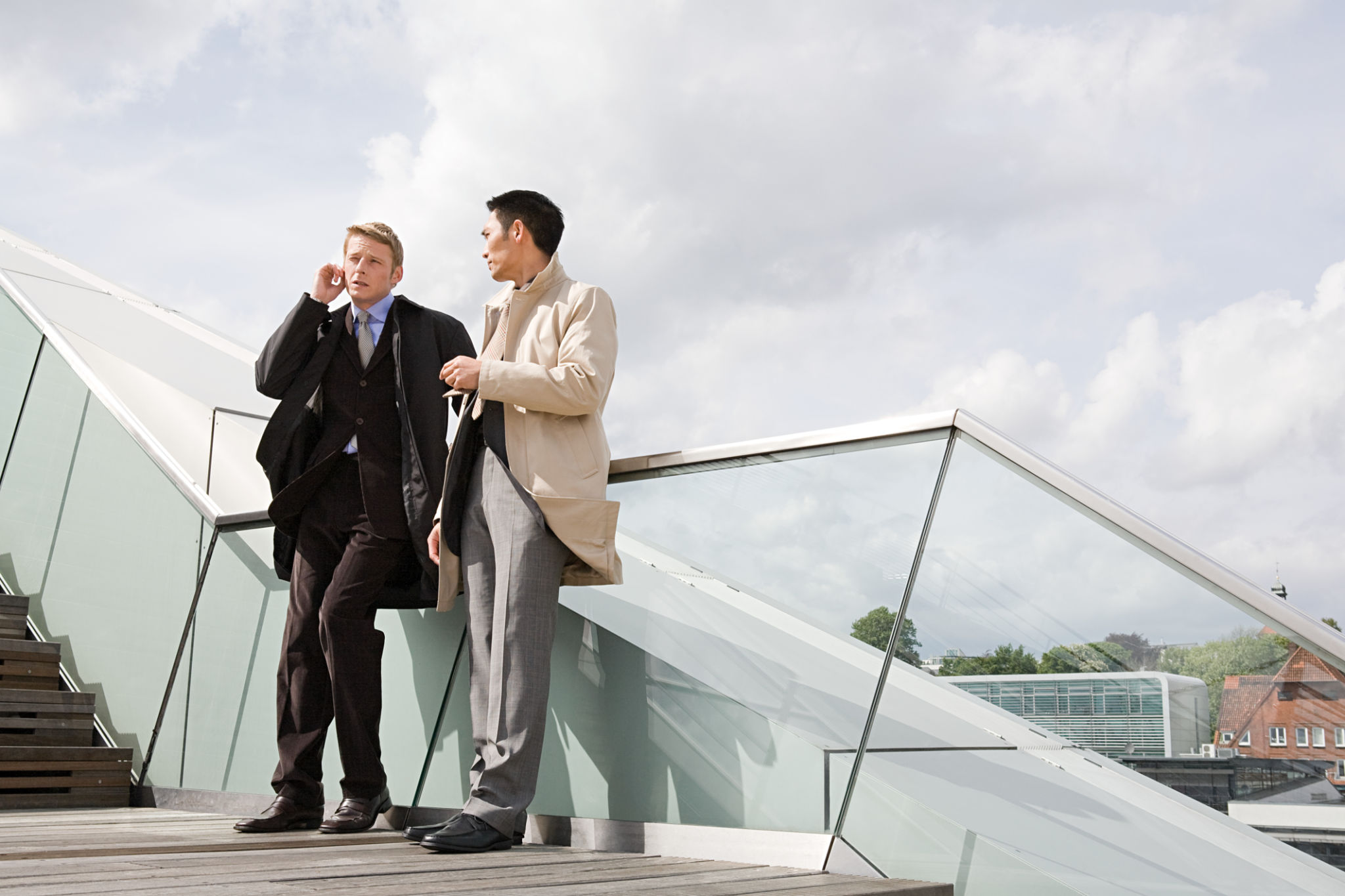
Conclusion: The Future of Mining with Simulation Modeling
The successful implementation of simulation modeling in this case study underscores its potential as a transformative tool in the mining industry. As technology advances, the capabilities of simulation modeling will continue to evolve, offering even more precise and actionable insights.
For mining companies looking to enhance their machinery performance, simulation modeling presents a compelling option. By embracing this innovative approach, companies can achieve significant improvements in efficiency, cost savings, and overall productivity, paving the way for a more sustainable and profitable future in mining.